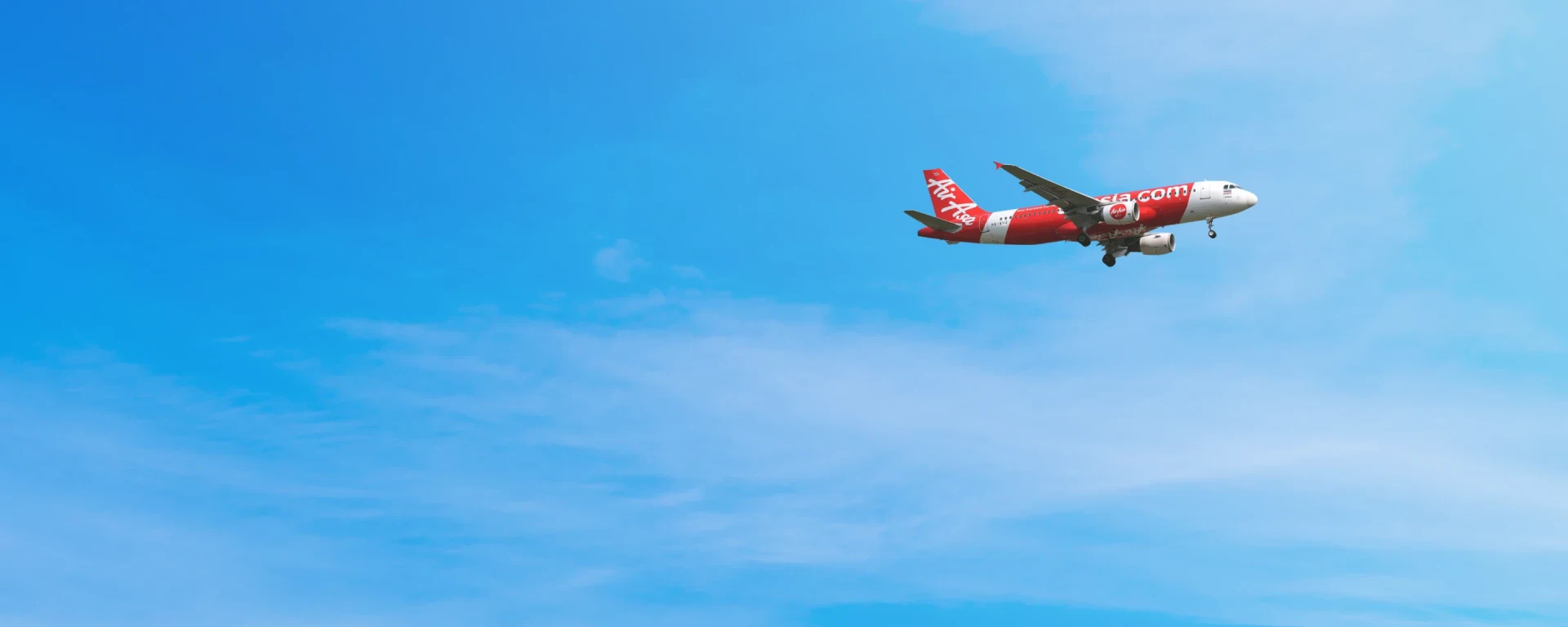
Environmental Management
Thai AirAsia established a Sustainability Working Group comprising Heads of departments to ensure lines of accountability in attaining our sustainability objectives and targets. A key duty of the committee is environmental management through the suppression of pollution and carbon emissions generated by our operation. The Principle of Sustainability serves as the basis for the committee.
Key Performance
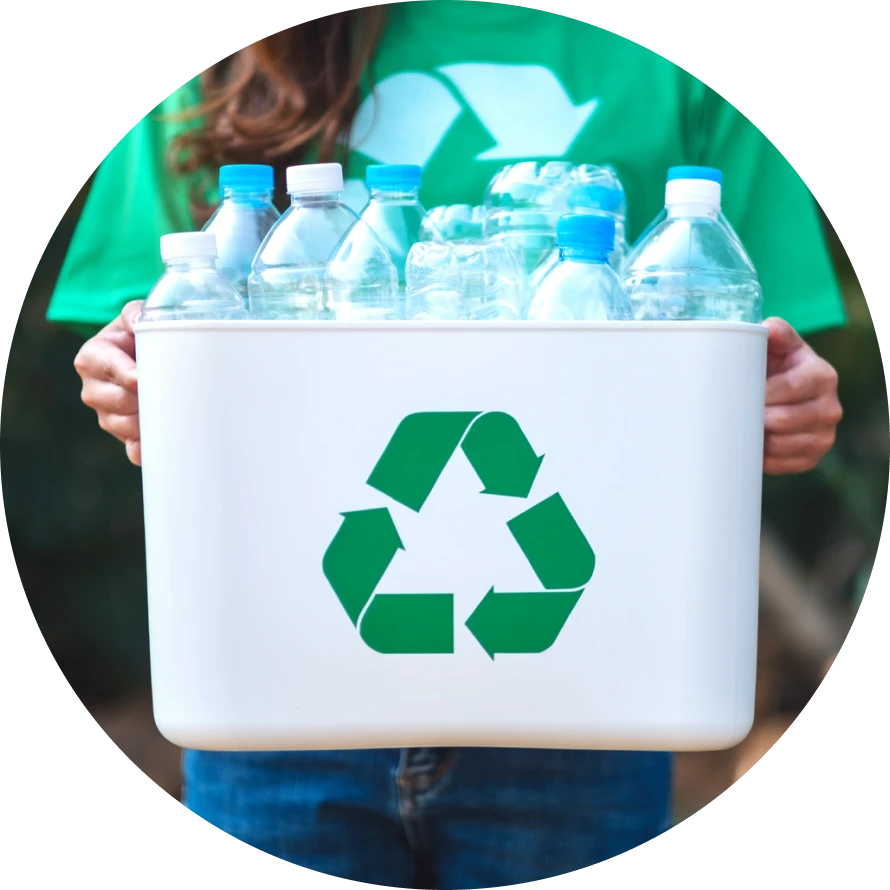
Waste Management
Efficient management of waste from our business and daily operations is a key focus in our environmental management. Thai AirAsia aims for zero waste to landfills and has created a network of partners for maximum waste management efficiency to achieve this target.
1. Non-Hazardous Waste Management
The majority of the Company’s non-hazardous waste comes from In-flight catering, including fresh and dried food as well as packaging. Approximately 260,000 pieces of waste are generated annually which is equivalent to 33% of the total quantity of food and beverages available for In-flight Services.
Meals and Product uplifted for Servicing and Selling per year
In accordance with International Catering Waste requirements, all fresh meals taken aboard flights, whether consumed or not, may not be cycled back into service with the exception of dried food items. Catering waste generated by the airline returned along with refuse to warehouses is sorted into different types, such as plastic, aluminium, paper, and other. The RAMP Department forwards the waste to JDP Technology, a company that further sorts and separates the refuse so it may be properly processed. The majority of recyclable waste is recycled back into plastics and aluminium while the remainder is converted into animal feed or industrial fuel.
Results and Targets
We achieved the target with a
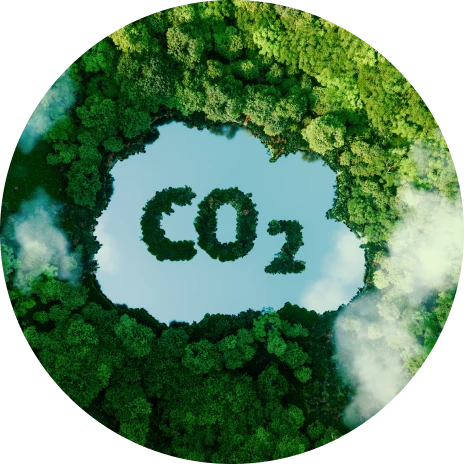
The Company reduced its CO2 emissions by
Equivalent to the planting of
equivalent to cars with a 50-liter fuel tank capacity
2. Hazardous Waste Management
Hazardous waste generated by the Company’s aircraft maintenance includes aluminium chemical and lubricant cans and materials such as glues, sealants, gloves and light bulbs. The Company follows AOT protocols in sorting and disposing of each type of waste at designated areas within airports. In 2024, a total of 10,696 kg of hazardous waste was sorted and disposed of in accordance with AOT protocols. Furthermore, the Engineering Department carries out detailed analysis of equipment usage in aircraft maintenance and plans usage through Google Suite to minimise waste.
Results and Targets
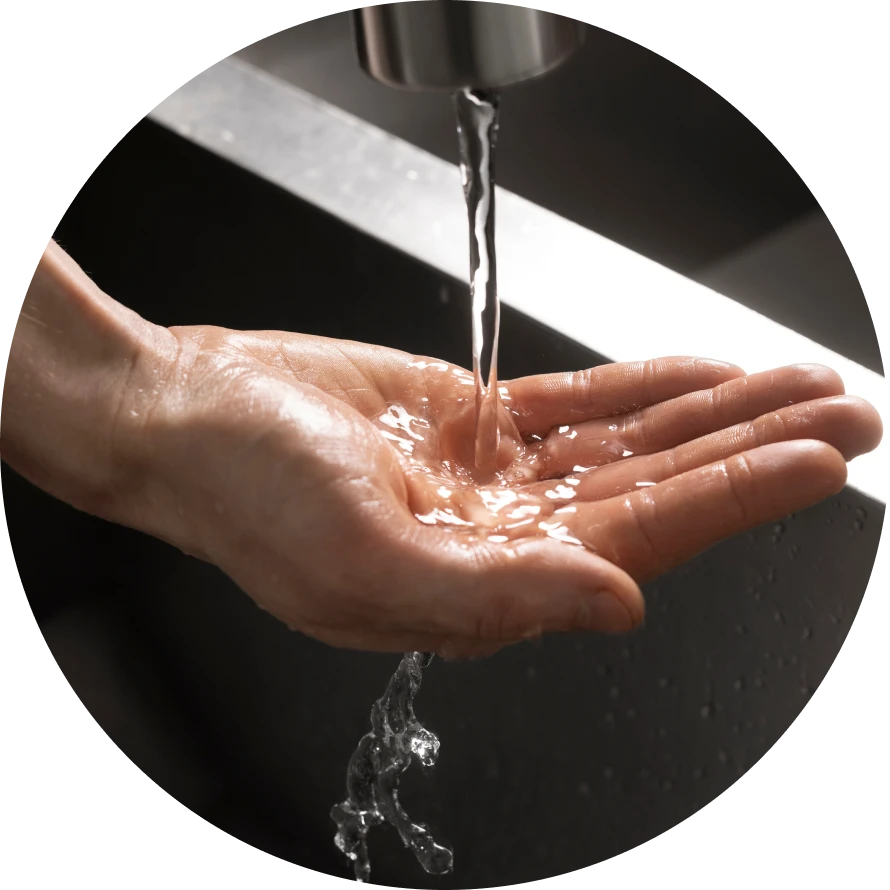
Water Management
Thai AirAsia manages its water resources for optimum efficiency. The Company monitors, tracks, and analyses the amount of water consumed in each of its operational areas and on flights while also working to recycle water from processes for maximum utilisation.
Ground Operation Water Resources
Since 2019, Thai AirAsia has maintained targets for the use of water in ground operations. The Company analysed and evaluated the consumption of water for ground operations and constructed a sustainable airport water treatment station to improve efficiency and better regulate the quality of water resources.
Water Consumption on Domestic Flights (litres per flight): Target of 100 litres per flight
Strategies to Reduce Water Consumption
Ramp and Ground Service analysed flight duration from origin to destination and passenger water consumption on flights to improve water management. The Company targeted reducing the refill of water for domestic flights from 100% to no more than 50%, or less than 100 litres per domestic flight compared to the usual 200 litres. As a result of efforts in 2024, the Company was able to achieve an average water refill of less than 100 litres per flight. Average consumption of water on domestic flights this year was 56.2 litres per flight, making refills sufficient for passenger usage. Maximisation of water usage was also in line with Company environmental policies.
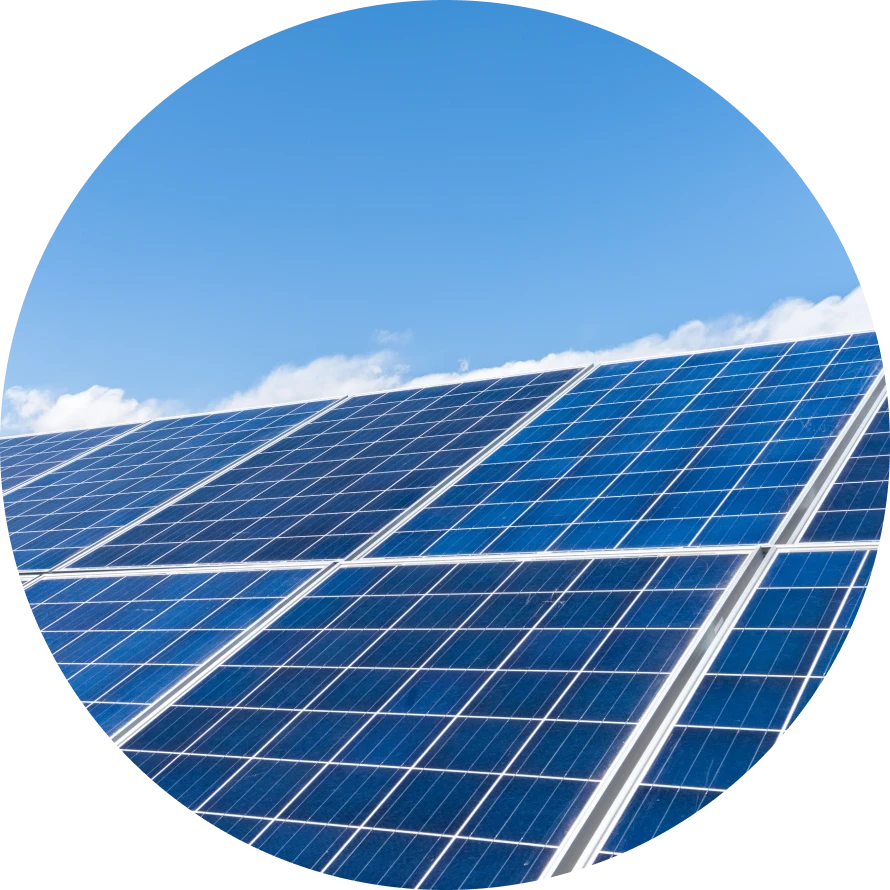
Energy Management
The Thai AirAsia energy management plan this year involved the installation of programs and equipment for the management of our chiller plant. The additions improved the efficiency of the plant in alignment with demand in our offices during different time periods. At the same time, we sought to reduce energy consumption and human error while increasing the accuracy of the chiller plant’s operation. The effort was initiated at AirAsia Academy.